1 概述
百菌清是一种广谱、高效、低毒、低残留的农林用杀菌剂 ,可防治多种农林作物的真菌病害 ,具有保护和治疗的双重作用 ,并可用于工业防霉杀菌、水果保鲜等。我厂的 1 0 0 0t/a百菌清工业性试验装置于1 986年 3月破土动工 ,该装置的两个主要生产工序 ,“氨氧化”于 1 988年 8月建成并于当年 9月 2 9日投料试车 ,“氯化”于 1 988年 1 2月建成并于1 989年元月 2 5日投料试车。由于该装置的技术放大倍数高达 1 0 0 0倍 ,给工业性试验带来了很大的困难。经过不断的技术改造、完善 ,装置于 1 994年元月通过了国家鉴定验收。国家鉴定验收委员会在肯定成绩的同时 ,要求尽快解决氨氧化废气处理等遗留问题。氨氧化废气中CN- 浓度高、含量起伏大 ,国内生产厂家一直在寻求彻底治理。我厂的氨氧化由于废气无法处理等原因 ,时开时停 ,不能正常生产 ,使生产百菌清的原料二腈一直依赖外购 ,导致百菌清成本居高不下 ,产品在市场上缺乏竞争力。因此 ,尽快根治氨氧化高浓度含氰废气 ,实现二腈自给 ,一直是我厂员工的共同心愿。
2 废气排放治理现状
2. 1氨氧化及其废气
2. 1. 1氨氧化反应原理
原料问二甲苯、氨、空气在氨氧化炉内发生催化反应,生成中问产品问苯二甲睛(简称二睛,代号TRN),同时有生成HCN的副反应。
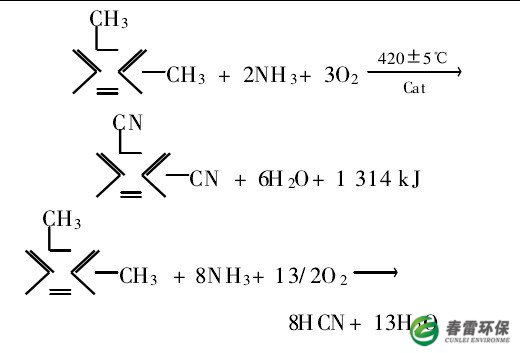
2.1.2氨氧化废气
氨氧化废气的主要有害成分为CN-,NH3和NOX,根据氨氧化试车时昆明市环境监测中心的测试报告,其浓度见表to
2.1.3氨氧化废气治理回顾
2.1.3.1原始设计的处理流程
氨氧化废气→水洗→加铁制黄血盐→蒸氨→加压水解→生化处理→排放

该处理装置虽已建成,但由于管道堵塞严重等原因,流程无法打通,使装置无法使用,一直闲置。
2. 1. 3. 2催化焚烧中试
(1)中试流程
采用杭州环保设备厂提供的“催化焚烧”装置,对氨氧化废气进行催化焚烧处理。由于该工艺在国内尚无先例,经双方协商先进行中试,成功后再放大。其中试流程为:
氨氧化废气→过滤→多层催化焚烧→冷却器→引风机→排放

由表2可见,催化焚烧后,CN一和NH:排放浓度和排放量明显降低,但是氮氧化物又明显增加,产生了新的二次污染物。
(3)催化焚烧的不足之处
该工艺需采用不同催化剂,在不同温度下对不同的废气组分进行催化焚烧,焚烧炉温度控制困难、操作维护复杂、运行可靠性差。由于催化剂
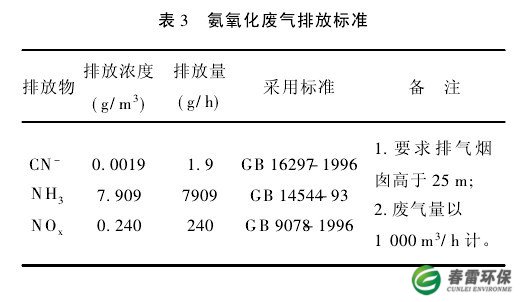
昂贵及寿命有限,造成运行费用高。同时,虽然催化焚烧后CN一和NH:明显降低,但仍然不能完全达标排放,并且又使污染物NO、显著增加,需再次治理。
2. 2氯化及其废气
2. 2. 1氯化反应原理
中问产品二睛和氯气在“流化赓固定床”复合反应器内发生置换反应,生成最终产品四氯问苯二甲睛(俗称白菌清,代号TPN)。
2. 2. 2氯化废气
氯化废气中的主要有害成分为反应产生的氯化氢和未反应的氯气。经过多年的生产实践,不断改造完善生产工艺,氯气单耗明显降低,由原来的6t降到现在的2t,废气中的氯含量由原来的30%降至现在的2%以下。
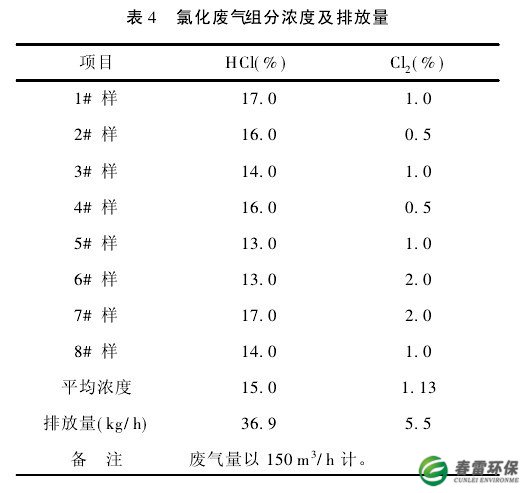
2. 2. 3氯化废气治理回顾
2. 2. 3. 1回收废氯,制三合一盐酸,多余的废氯用电石渣液吸收
氯气单耗为6t时,由于废气中氯气含量高,大部分废气经压缩输送至远离主反应装置(约800 m)的三合一炉,和氢气反应经水吸收制成合格盐酸.剩余废气用石灰乳(后改为电石渣)吸收处理。其处理流程为图3。
2. 2. 3. 2直接用电石渣吸收处理
经不断技改,废气中的氯气含量降至2%以下,已无法再用三合一炉回收其中的C 12,氯化废气经压缩后直接送至1000m远的废气塔,用电石渣[主要成分为C a( OH ) 2]吸收处理后排放。
3氨氧俗氯化废气综合治理方案
3. 1综合治理方案及流程
将现在直接排放的氨氧化废气并入氯化废气系统,集中用电石渣进行氯氧化反应处理。
氯化废气和氨氧化废气分别经风机加压后进入混合器混合,经废气塔和电石渣逆向接触吸收后排放,废液在废液池内经充分搅拌反应后用泵打至电石渣场。
3. 2反应原理
在混合器内,氯化废气中的氯化氢和氨氧化废气中的氨发生中和反应,生成氯化铰。
HC1+ NH3= NH4C1
在废气塔和废液池内,发生一系列化学反应:
(1)废氯气被电石渣吸收,生成次氯酸钙(漂白粉)
2Clz+ 2Ca(OH)z= C a( 0 Cl) z+ CaClz+ 2H z0
( 2) CN一和次氯酸钙反应,先生成氯化氰
C N-+0 C-+Hz0 }NCI+ 20H-
氯化氰在电石渣的碱性环境中发生水解反应,生成氰酸根(CNO)。
CN 0-毒性仅为CN一的1/ 1 000,对鱼致死量为125一 250 mg/ L,已经基本达到排放要求。
CNC1+ 20H-=CNO一+C1+Hz0
一般生成CN 0一为局部氯氧化阶段,理论上,CN一:C12 Ca0= 1: 2.73: 2. 15。
( 3)若次氯酸钙足量,CNO一继续分解,被彻底分解成毒性甚微的CO:和Nz
2CN 0一+30C1+Hz0=
2COz+ Nz+ 3C1+20H
生成N:和CO:为完全氯氧化阶段,理论上CN-:Clz= 1: 6.830
3. 3预期治理效果
3. 3. 1简化氯化废气处理
可取消现有的废气压缩装置,使氯化废气处理工艺流程缩短简化。取消氯压机(110 kW)后,无物料(硫酸)消耗,运行电费和维护费用大幅度降低,每年至少减少白菌清生产费用10万元。
3. 3. 2氨氧化废气可基本达到排放要求
氨氧化废气中的CN一和氯气、电石渣反应后分解成毒性很小的CNO-,甚至CO:和Nz,基本达到排放要求,这就为氨氧化装置的长期稳定生产,提供了前提和保证。
4讨论
1)取消氯压机后,废气输送的动力拟用风机来提供,风机输送电耗小,风压低,很适合白菌清要求微负压生产的需要,但必须简化缩短废气管道,将远离主反应装置的氯化废气处理搬迁至现在的氯压机岗位,改建成新的废气氯氧化处理装置,集中处理氯俗氨氧化废气。电石渣液可用泵输送直接打入废气塔后进入废液池,处理废气后再用泵打回电石渣场,即使处理后废液中CN-略有超标,也会在渣场内被电石渣吸附,不会排入下水造成污染。
2) C N-分解成CN 0-需要一定时问,在设计时应充分考虑废液池的容积,使废液在连续搅拌条件下停留接触0.5~2h,促使CN-氧化分解。
3)一般处理要求氯氰重量比控制在4左右,应在废气塔底部接通新鲜C 1z,根据废气量适时通入适量C 1z来达到要求。
4)应调控好废液池内废液pH值,当ph>10时,CNC1很容易水解成CNO-。若需CNO-进一步分解,则声值要降至7. 5~8,因此要消耗酸(实际生产中为降低处理费用,一般很少采用此步骤)。
5)由于氯化和氨氧化废气中均含有较多的粉尘颗粒,会对风机输送造成不良影响,所以应在风机前设置过滤器。
6)该装置建成后,在下列三种情况下均可达到处理要求:
(1)氨氧俗氯化装置同时运行时,根据氯化废气的氯气量和氨氧化废气的CN一量,适时通入适量Clz;
(2)氨氧化装置单独运行时,根据氨氧化废气量,通入新鲜氯气,促使氯氧化反应发生;
( 3)氯化装置单独运行时,因无氨中和氯化氢,应加大电石渣液的浓度或流量,使废气中的C 1z和H C1完全被电石渣吸收。】
5结论
综合治理方案充分利用氨氧化和氯化的废气组分,立足现有装置和设备,以废治废,综合治理,用较低的投资和较少的运行费用,使较难处理的
氨氧化高浓度含氰废气,在氯化废气中的C}和电石渣的作用下,反应生成毒性较小的氰酸钙,可使氨氧化废气基本达到排放要求,为氨氧化装置的长期正常生产清除了环保上的最大障碍。